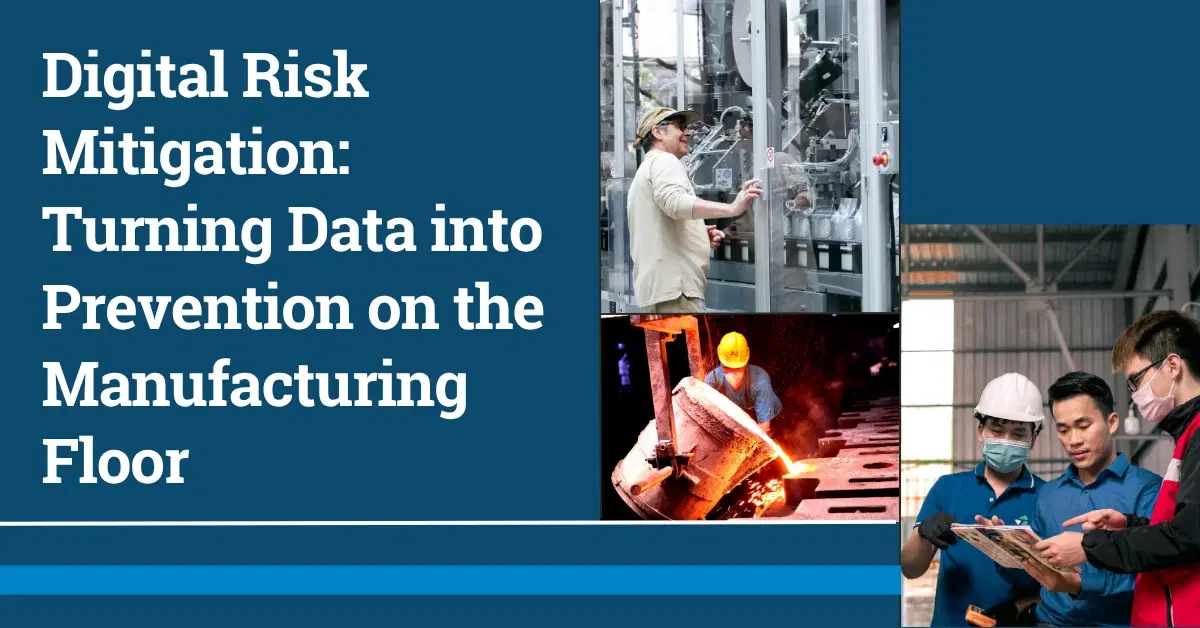
Digital Risk Mitigation: Turning Data into Prevention on the Manufacturing Floor
In truss and lumber manufacturing, the pace rarely lets up. Machines run nonstop, tools stay in motion, and teams push hard to meet hourly production goals. Even a small defect or quick equipment slip can throw everything off. Just one missed issue can throw off an entire shift, lead to expensive rework, or set deliveries back.
That's where tools like QualityReports.ai truly help teams stay ahead and in control.
By giving teams live access to inspection data, production patterns, and early warning signs, they can respond quickly, fix issues at the source, and keep operations running smoothly.
We'll look in this article at how digital inspections, analytics, and smarter reporting are helping manufacturers improve consistency and build a stronger, more proactive approach to risk on the shop floor.
What is Risk Mitigation?
In a manufacturing industry, Risk Mitigation means identifying what could go wrong and putting real solutions in place to stop it before it does.
For a lumber plant, it might mean catching a recurring misalignment before a hundred trusses are built out of spec. In light manufacturing, teams might notice that a certain machine consistently underperforms during the third shift, increasing product rejections.
Staying Ahead of Risk: From Fixing Problems to Preventing Them
Let's say your QA inspector flags a cracked connector plate on a finished truss. Traditionally, that might trigger a manual investigation, by which time, a dozen more have rolled off the line with the same issue.
With a tool like QualityReports.ai, that defect is instantly logged and visible to managers, supervisors, and even maintenance. If it's a tooling issue, production can be paused before more errors occur. That's real-time risk mitigation, not just catching problems, but stopping them in their tracks.
Here's how smart manufacturers are building better risk strategies using data:
Inspections That Keep Pace with Production
Manual checklists and clipboards can't keep up with the demands of modern manufacturing. Today's floor teams rely on tablets and mobile devices to capture quality checks in real time, creating digital records that are timestamped, consistent, and instantly accessible.
In a truss plant, that might mean verifying heel heights or plate placements mid-line, allowing teams to spot and resolve issues before they impact final assembly.
Detecting Patterns, Not Just One-Offs
It's easy to miss when a machine gradually falls out of alignment, but even small inconsistencies can lead to costly defects over time. These slow-building trends often appear in the data, like a recurring pattern of cutting errors or a rise in fastener issues during certain shifts.
By comparing data across shifts, materials, or equipment, the system helps uncover risks before they cause production loss or client dissatisfaction.
Actionable Feedback That Drives Change
Operational insights from frontline teams are often overlooked or lost in disconnected systems. QualityReports.ai establishes a continuous feedback loop that ensures critical observations translate into measurable action.
When a risk is identified, corrective actions are documented, assigned, monitored, and verified---creating accountability and closing the loop on quality issues.
Why Digital Risk Mitigation Isn't Optional Anymore?
The speed of modern manufacturing leaves no time for guesswork. Whether you're building engineered wood products or assembling light industrial components, you're under pressure to meet tight tolerances, fast turnarounds, and strict regulatory standards.
Staying reactive is expensive. That's why leading manufacturers are making digital risk mitigation a core part of their strategy. It helps them:
- Lag Time: Issues are often discovered after production runs, not during. The damage is already done.
- Inconsistent Data: Handwritten forms vary by inspector, shift, or site---leading to unreliable analysis.
- No Feedback Loop: Problems get reported, but patterns go unnoticed because the data isn't centralized.
- Slow Escalation: Safety flags or equipment defects take days to reach decision-makers.
And perhaps most importantly, it gives your team the confidence to act, knowing their observations won't disappear into a spreadsheet void.
How Does Risk Mitigation Software Actually Help?
Think of risk mitigation software as the quiet assistant working behind the scenes to keep production on track. It's not just a data repository---it actively helps you spot trends, flag recurring issues, and support continuous improvement.
Real-Time Inspections
Whether it's a cracked 2x4 on a press table or a crooked stud on a prefab line, real-time inspections let workers flag issues the moment they happen. These reports are synced instantly across devices---no need to pass paper, send texts, or wait for debriefs.
Alerts & Escalations
Trigger alerts for high-risk inspection results. For example, if two fall protection violations are logged within 24 hours, a safety supervisor is automatically notified. It's an early-warning system that reduces the chance of repeat problems.
Risk Tagging
Assign specific risk types to each inspection finding---structural, safety, equipment, procedural---allowing your analytics to reveal exactly where problems are coming from.
Trend Analysis
Instead of sifting through stacks of forms, teams can now view visual dashboards that surface emerging risks: repeat failures by asset, frequent fallbacks by shift, inspection scores by supervisor.
That's real mitigation---not just catching problems, but understanding what's causing them.
By organizing inspection data, it sends timely alerts, and gives your team a clear, actionable view of what's happening, without the clutter of confusing dashboards or extra admin work.
A Roadmap for Putting Risk Prevention into Practice
Starting small can lead to big changes. Here's how teams often begin the shift from reactive to preventive:
-
Digitize Your Inspections: Replace paper checklists with mobile-based inspections to ensure speed and accuracy.
-
Start Logging Everything: Even small inconsistencies matter. More data = better insights.
-
Analyze, Don't Just Archive: Use analytics to understand not just what happened, but why, and when it's likely to happen again.
-
Take Action and Track It: Make sure follow-ups are logged, resolved, and reviewed. That's how change sticks.
-
Expand Smartly: Roll out improvements to other teams or plants based on success stories, not guesses.
Why Teams Choose QualityReports.ai?
QualityReports.ai wasn't built for corporate box-checking. Tools like this are created for manufacturers, including QA techs checking every third truss, supervisors managing tight schedules, and plant managers committed to timely deliveries.
Here's what sets it apart:
- Real-time inspections, not after-the-fact reports
- Customizable inspections for lumber, truss, prefab, and more
- Seamless corrective action workflows
- Built-in analytics that frontline teams can actually use
Whether you're overseeing a single facility or multiple sites, having timely insight and the right systems in place helps teams catch risks early, address issues efficiently, and maintain consistent output.
Prevention Is the New Standard
Effective risk mitigation on the manufacturing floor means moving beyond reacting to problems; it's about preventing them with real-time data and intelligent tools like QualityReports.ai.
This kind of approach helps teams spot issues early, reduce costly disruptions, and maintain consistent product quality.
By embracing these modern strategies, manufacturers can improve efficiency, protect their bottom line, and build a culture focused on continuous improvement. That's the future of manufacturing risk management and with QualityReports.ai, it's already within reach.
Schedule a demo today with QualityReports.ai and see how digital risk mitigation can transform your production process.