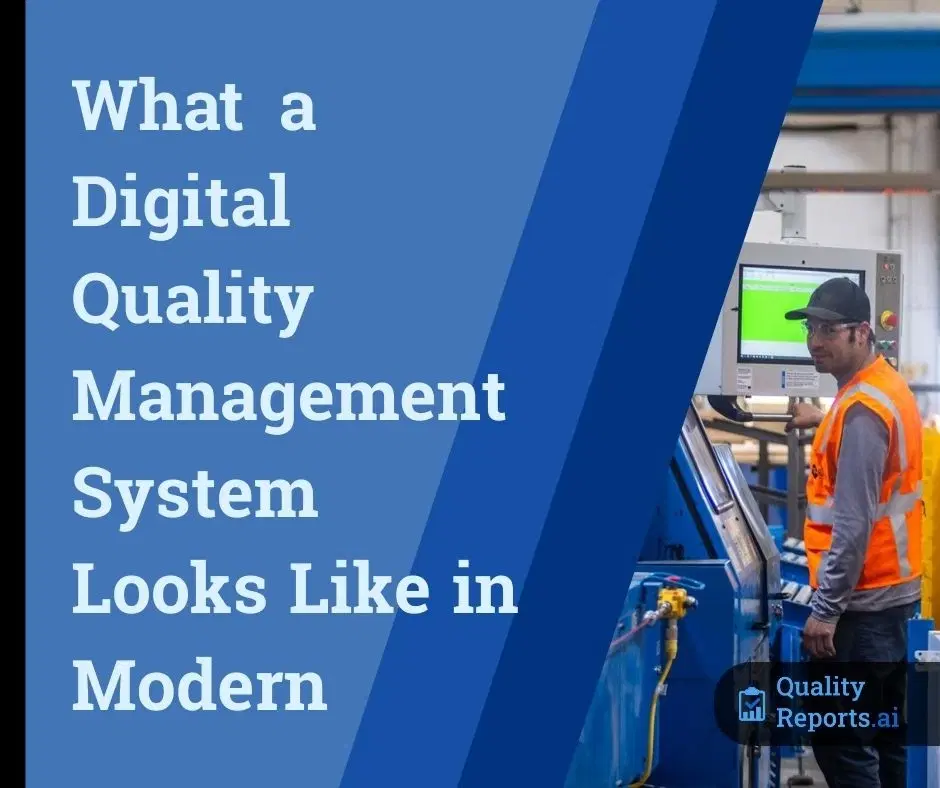
What a Digital Quality Management System Looks Like in Modern Manufacturing
When it comes to lumber and truss, quality management isn't handled by consultants, it's handled on the shop floor, in the yard, and on the line. The stakes are simple: get it right, or it costs you wasted material, failed loads, and rework that drags down every shift.
Most manufacturers have a quality system in place. But if it still relies on binders, paper forms, and scattered spreadsheets, it's probably creating more blind spots than clarity. A modern Quality Management System (QMS) doesn't just document problems, it helps you prevent them, fix them fast, and prove it when someone asks.
In this article, we'll walk through what a digital QMS actually looks like for a manufacturer, not in theory, but in practice, and how tools like ours at QualityReports.ai can plug directly into how you work now without forcing a full system overhaul.
What Is a QMS and What's Changing?
At its core, a QMS is a framework that helps you control, monitor, and improve product quality across your operation. It's the engine that keeps SOPs enforced, inspections flowing, and accountability clear. Whether you're dealing with third-party compliance, internal quality standards, or simply trying to reduce scrap, the QMS is what keeps your process on track.
The problem is that traditional QMS implementations weren't designed for speed. They rely heavily on static documentation and disconnected tools that make real-time execution difficult. In fast-moving, hands-on environments like lumber and truss production, that disconnect costs time and consistency.
The Hidden Costs of Paper-Based QMS Execution
Most manufacturers still run part of their quality process on paper, daily checks, incident reports, and inspection logs. And while it may feel familiar, it slows everything down. When data lives in filing cabinets or lives on one person's clipboard, it's not part of your system. It's a liability.
Paper-based systems break down in three major ways:
- They create time lags between when an issue is spotted and when it gets addressed.
- They block visibility across shifts, departments, and sites.
- They make analysis and trend-spotting almost impossible without heavy manual work.
Digital tools solve these problems not by reinventing quality, but by putting execution where it needs to be; live, mobile, and connected.
What a Digital QMS Looks Like on the Floor
A modern QMS doesn't mean adopting bloated software or re-engineering your process. It means using tools that keep your standards alive across every shift, every site, and every employee. Here's how that plays out in real operations using QualityReports.ai:
Inspections That Move with the Work
Forget static forms or Excel-based logs. With QualityReports.ai, inspections are done directly from the floor. Accessible from a tablet, phone, or desktop, using forms that reflect how your work is actually done.
You can build checklists that cover machine checks, material inspections, process steps, or anything else. Need photos for verification? Built-in. Want to trigger follow-ups when something fails? That's built in too.
It's not about checking boxes, it's about building a system where every inspection feeds your quality engine in real time.
Enforcing Procedures Without Slowing Teams Down
Support procedures like calibration checks, shift changeovers, or safety validations are often informal or inconsistently applied. A digital QMS keeps them on track by making these workflows part of your daily rhythm.
Supervisors can assign and verify procedure completion. You can even embed references like SOPs or safety protocols directly into the form so the guidance is there when it's needed, not buried in a binder.
The result? A system that drives consistency without bogging teams down.
Real-Time Visibility for Quality Leaders
With every inspection and procedure logged digitally, your data stops sitting idle. You get live dashboards that show what passed, what failed, who flagged it, and where it happened.
This kind of visibility changes how you manage:
- Spot repeated issues before they become systemic.
- Track SOP compliance across teams or locations.
- Quickly respond to failed checks with documented follow-ups.
Instead of monthly reports and lagging indicators, you're looking at live quality health.
Connecting It to Your Larger QMS Framework
If you're already operating under a QMS framework, like ISO 9001, ANSI/TPI 1, or your own internal system, QualityReports.ai doesn't replace it. It powers it.
Think of it as the operational backbone. You've got procedures. You've got standards. QualityReports turns those into real-world workflows and gives you a trail to prove it. Whether you're preparing for a customer audit or investigating a line issue, everything's documented, traceable, and actionable.
Why This Works for Lumber and Truss Operations
You don't need another enterprise tool, you'll use 10% of. You need something that fits the way your team already works, hands-on, fast, and focused on output.
QualityReports.ai was built for environments like yours. It doesn't try to be everything, it focuses on inspections, procedures, and analytics. That means:
- Your leads and operators can use it without hours of training.
- Your managers get immediate visibility into what's happening.
- Your quality team gets data they can act on and prove with.
And most importantly, you stop running blind.
Final Word
A quality system that lives in a binder is a liability. A quality system that lives in real-time workflows? That's a competitive advantage.
Whether you're trying to tighten up inspections, prep for a customer audit, or just bring more consistency to your operation, a digital QMS is one of the smartest upgrades you can make.
Start building yours at QualityReports.ai, no overhaul required.