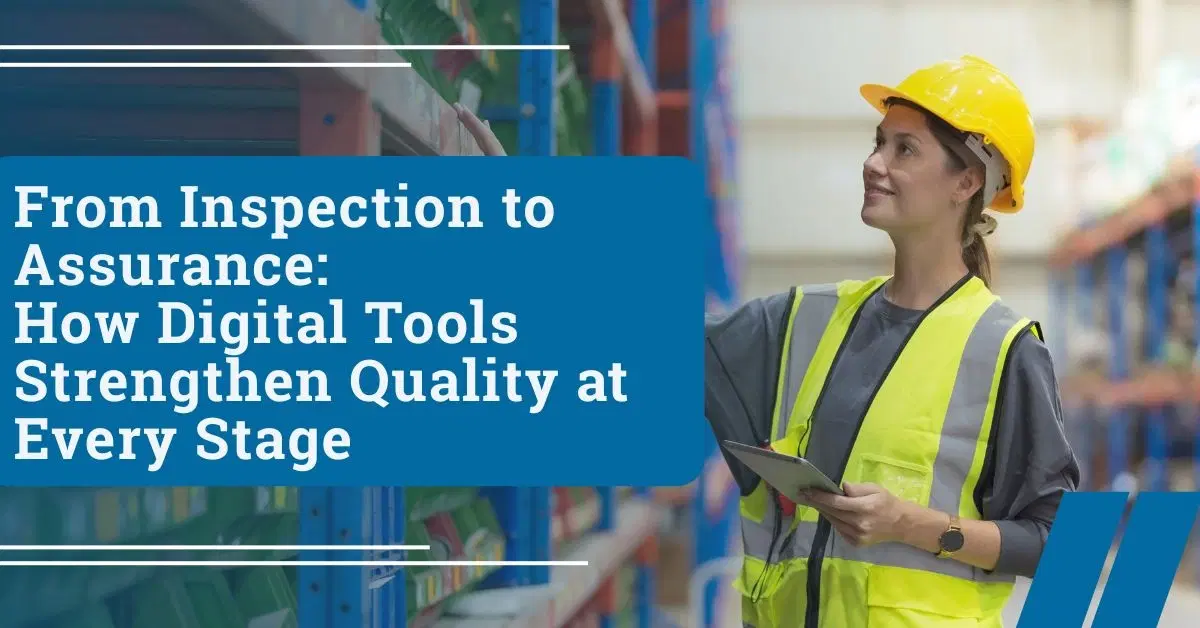
From Inspection to Assurance: How Digital Tools Strengthen Quality at Every Stage
Quality can no longer be a final stage. It is not a case of ticking boxes, but rather finding out possible problems before they affect performance. Spreadsheets and paper checklists are outdated, and they cannot keep up with the challenges as businesses expand.
The QA of today is all about building reliable systems, collecting valuable data, and making it simpler to transition between problems and solutions. Tools like ours at QualityReports.ai make this possible by streamlining how teams manage inspections, monitor quality, and respond to problems---without the delays caused by manual processes.
This article explores how digital QA tools are transforming quality management, from the first inspection all the way through to full operational assurance.
What Is Quality Assurance?
Quality assurance is the systematic processes that are established to make sure that services, products, or processes are in line with certain requirements. Quality Assurance is a preventive measure unlike quality control that is concerned with detecting defects in the final output.
Well-designed QA systems give teams the tools to:
- Establish clear quality standards
- Monitor performance across multiple stages
- Spot and correct problems in advance
- Remain industry and regulatory compliant
Quality assurance does not only mean avoiding errors. It is about reinforcing processes and making reliable results at scale.
Quality Control vs. Quality Assurance
The distinction between quality control vs. quality assurance may be useful in explaining why contemporary QA tools are more than just inspection tools.
Feature | Quality Assurance | Quality Control |
---|---|---|
Purpose | Prevent Defects | Detect defects |
Approach | Proactive, process-driven | Reactive, product-driven |
Timing | Throughout production | After production |
Responsibility | Shared across departments | Primarily handled by QA/QC teams |
Examples | Process audits, workflow validation | Final product checks, defect analysis |
Traditional control methods may still play a part, but scalable assurance relies on smart systems to maintain standards consistently across people, places, and time.
Why Manual QA Can't Support Modern Compliance and Quality?
Manual methods like using spreadsheets for audits or emails to flag non-conformance can work on a small scale. But they often lead to:
- Missed inspections or incomplete documentation
- Delayed follow-up on issues
- Inconsistent data across teams
- Difficulty demonstrating compliance during audits
Outdated or inefficient quality processes can affect everything from safety and service standards to customer trust and brand reputation. To keep up, a more agile and data-connected solution is essential.
How Digital Platforms Like QualityReports.ai Strengthen Quality Assurance?
The new generation of QA platforms such as QualityReports.ai provides an intelligent, organized way of quality management. Teams obtain a unified system where the inspection forms, real-time performance data, corrective actions, and reporting are united, and quality assurance become more consistent, scalable, and repeatable.
1. Advanced Digital Forms
Traditional paper checklists are vulnerable to errors and inconsistencies. Digital forms reduce these risks by:
- Standardizing data collection across teams and locations
- Adapting dynamically to inputs using conditional logic
- Automatically saving data for instant access and retrieval
This boosts accuracy at the frontline and ensures that inspections are thorough---eliminating lost paperwork and incomplete submissions.
2. Real-Time Insights
Rather than waiting on static, delayed reports, managers can access live dashboards that:
- Display QA activities as they occur
- Identify compliance gaps or recurring issues
- Monitor team performance across departments
With real-time visibility, leaders can make faster, data-driven decisions and address quality issues proactively.
3. Automated Corrective Actions
Unresolved quality problems may cause delays or reoccurring problems. Digital Quality Assurance workflows assist in the following ways:
- Automated follow up actions when problems occur
- Delegation of duties to the right team members
- Monitoring and checking of tasks completion
This will make sure that every problem is not only recorded but also resolved, and this will effectively complete the quality management loop.
4. Centralized, Audit-Ready Records
Any form, update, and time stamp is safely stored in a single location. Teams can easily access all complete and verifiable records when audits or internal reviews are required, and the scramble is removed, and audit confidence is gained.
Bringing Quality Assurance into the Digital Age of Software
Software Quality Assurance (SQA) is the most important aspect of making applications reliable, secure, and high-performing, not only during the launch, but also during the whole lifecycle.
The contemporary SQA tools and practices enable development teams to:
- Catch bugs early with automated testing
- Ensure that the code passes important performance, security, and compliance requirements
- Keep traceability using version control and keep documentation in place
As with any other industry (manufacturing or service), when we apply QA principles to software we can prevent expensive reworking, increase long-term stability and create systems that will last.
The Value of Scalable Digital QA Systems
Modern QA platforms do much more than just digitise inspection checklists. They provide a unified structure that promotes accountability, drives improvement, and ensures visibility across the organisation. Here's how:
Quicker Resolution of Quality Issues
- Automated workflows make it easier to assign tasks, track progress, and close the loop---so nothing slips through the cracks.
More Accurate and Consistent Data
- Smart digital forms reduce human error, enforce standardised input, and lead to higher-quality data you can rely on.
Stronger Team Ownership
- Every submission and update is time-stamped and linked to a user, reinforcing responsibility and making quality everyone's job.
Simplified Compliance
- With centralized, well-organized records, preparing for audits or meeting regulatory demands becomes faster and far less stressful.
Built-In Scalability
- Whether you're expanding teams, opening new sites, or growing globally, digital QA systems scale easily without reinventing the process.
By minimizing manual work and linking data across departments, these platforms free up teams to focus on what matters most: consistent, ongoing quality improvement.
Aligning with Recognized Standards
Digital QA platforms also help organizations align with established quality and safety frameworks. These include:
- ISO 9001: International quality management guidelines
- FDA Quality System Regulation: Essential for medical and biotech compliance
- OSHA Guidelines: Workplace safety and health standards
- EPA Recordkeeping Rules: Applicable in environmental compliance tracking
Integrating these requirements into daily workflows is much easier with digital platforms designed to capture, track, and report everything in one place.
Take the Next Step in Quality Assurance
Those days when we can only count on end-stage inspections are over. A side process is no longer called quality assurance; it is the pillar of operational excellence.
Quality programs are changing the way teams collect data, solve problems, and operate with high standards with the help of digital tools such as QualityReports.ai that introduce structure, speed, and scalability to quality programs.
Digital QA can help you keep manufacturing lines, facility inspections, and safety measures more connected and accountable, whether you oversee the whole system or a specific part of it.
See how QualityReports.ai can make your QA processes more efficient and bring actual results.
Take it for a Test Drive or explore our platform to experience it.