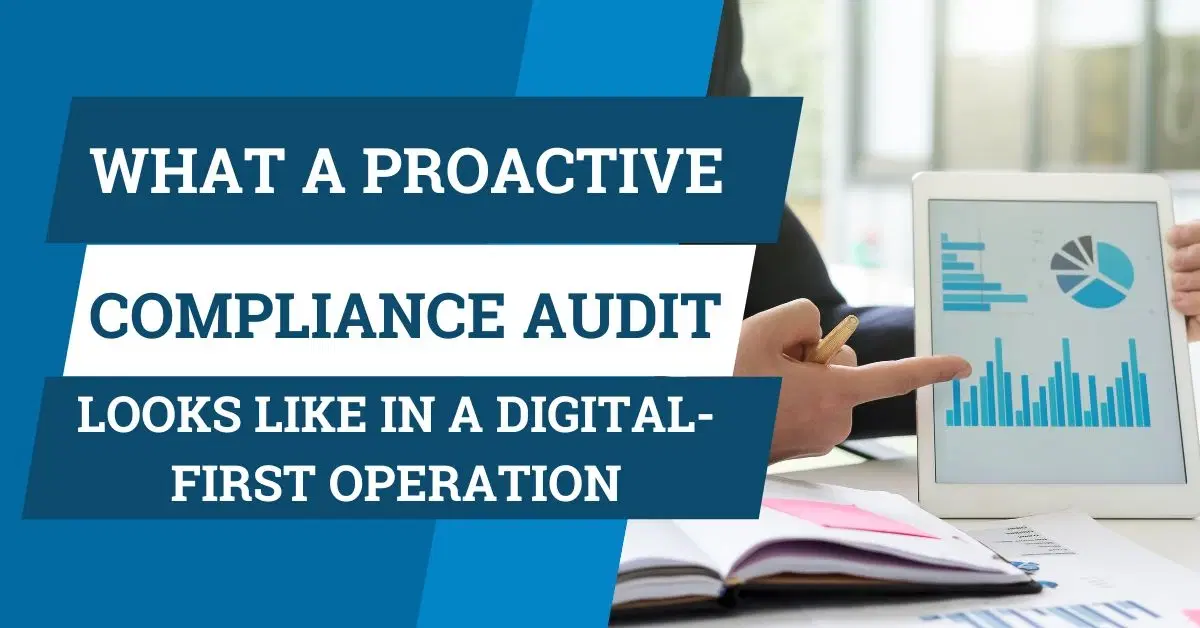
What a Proactive Compliance Audit Looks Like in a Digital-First Operation
Manufacturing leaders know that compliance is an ongoing commitment. Still, for many operations, audits remain a scramble. Teams rush to locate scattered documentation, verify outdated records, and pull together last-minute reports---often under pressure.
It's a reactive cycle that creates stress and leaves gaps at a time when compliance demands are only growing. This matters in industries like truss and lumber manufacturing, where safety checks, quality benchmarks, and documentation are part of the daily rhythm on the floor.
In these environments, compliance isn't something you do off to the side. It's threaded into the work itself, by how machines are set up, how teams move through their shifts, and how supervisors track what's been done. It gives teams the structure to stay ready and the visibility to keep getting better.
This article will show you how QualityReports.ai enables this shift by embedding real-time tracking, audit history, and compliance-tagged forms into routine workflows---so readiness isn't a sprint.
How Proactive Audits Work in Real Manufacturing Environments
A proactive compliance audit approach begins with how information is captured, verified, and retrieved across every level of the operation. It's about building a system in which compliance auditing is used, real-time, and reliably.
Every inspection, form submission, and training completion becomes part of a live compliance framework, especially in Digital-First Operation:
- Inspection logs are no longer static documents; they're timestamped, standardized, and compliance-tagged.
- Training records are not scattered across HR systems and file servers, and they're accessible by role, site, or certification.
- Corrective actions aren't closed verbally; they're tracked from issue to resolution with full accountability.
With the help of QualityReports.ai, the system captures all of this automatically, ensuring that documentation isn't assembled for audits, it simply exists within the workflow.
Risks of Outdated Compliance Methods
Traditional compliance approaches such as manual checklists, shared spreadsheets, and paper-based logs may have worked when regulatory demands were simpler. However, in a fast-moving manufacturing environment, these outdated systems create more risk than reliability.
The result? It will leave you open to missed inspections, costly penalties, and eroded trust with clients who expect clarity and accountability. In an environment where both regulators and customers demand more, sticking with old tools can quietly chip away at your competitive edge.
For example, the challenges facing a regional truss plant managing OSHA regulations for fall protection and powered equipment. The equipment may be inspected, and training may be delivered, but if these actions are not logged in a traceable, verifiable way, they don't hold up during an OSHA compliance audit.
Disconnected systems added pressures on plant managers, safety leads, and quality teams, who forces them to scramble for records and piece together data when audits come around.
This reactive posture confidence, consumes resources, and reduces time spent on forward-looking quality improvements.
Grounding Compliance in Real Manufacturing Operations
In truss, lumber, and structural material operations, compliance requirements depend on the specifics of each facility. From OSHA 1910.147 regulations on Lockout/Tagout to ANSI guidelines for saw safety---or even client-driven quality benchmarks.
For example, a truss production line used elevated platforms that may require to conduct weekly ladder inspections, monthly equipment calibration checks, and quarterly hazard communication refreshers. When these inspections are paper-based in different systems, verifying compliance across teams and shifts becomes inefficient and error-prone.
By contrast, tools like QualityReports.ai centralizes this activity. A safety coordinator can track all ladder inspections across locations, ensures audits are collected digitally, and filter logs by date or responsible team.
The Role of the Compliance Tracking Tool
Proactive auditing is a reliable compliance tracking tool. It's not just recording data, it ensures that data is audit-ready, connected to relevant standards, and presented in context.
QualityReports.ai supports this by:
- Tagging each form and record with the appropriate regulation or standard (e.g., OSHA, internal policy, ISO, or customer requirement).
- Maintaining audit trails that show who completed an action, when, and under which standard.
- Flagging noncompliant or overdue actions in real-time, giving teams the opportunity to correct issues before they escalate.
Instead of depending on memory or disconnected reports, teams have a single source of accuracy that reflects operational reality. Compliance moves from being a periodic disruption to a natural extension of production and quality control.
Effortless Oversight in High-Stakes Environments
One of the challenges in compliance implementation is avoiding added workload. Frontline staff are already balancing safety, output, and procedural adherence, which adds more manual logging risks, non-completion or resentment.
A digital-first system must therefore align with how teams already work. With QualityReports.ai:
- Equipment inspections can be performed via mobile, on-site.
- Issues can be flagged directly within the form, prompting corrective workflows.
- Supervisors can verify signatures and training without searching through binders or multiple drives.
How Audit-Readiness Strengthens Daily Operations
Proactive compliance does more than keep you on the right side of regulations; it also improves how your operation runs. When potential issues are seen early, they're addressed before turning into enforcement actions or production delays. That kind of foresight helps minimize downtime and keeps your team focused on productivity, not damage control.
Many commercial buyers require clear, consistent compliance records during vendor assessments. Having those details readily available and showing that your organization takes oversight seriously builds trust and positions you as a dependable partner.
Operational Excellence Starts With Proactive Compliance
When audits are approached as isolated events, they often bring unnecessary stress and disruption. But when compliance is embedded into daily operations, it becomes a source of stability that something teams can trust, not scramble to prepare for.
QualityReports.ai supports this transformation by making compliance seamless, consistent, and accessible across your entire operation. Instead of chasing paperwork, your teams can focus on doing the work right with confidence that the documentation is already in the right place.
In a manufacturing landscape where regulatory expectations and customer demands continue to evolve, proactive compliance isn't just good practice---it's a mark of operational excellence and a clear edge in a competitive market.
Take a closer look at how QualityReports.ai can make compliance effortless and audit days routine. Start exploring the platform now.