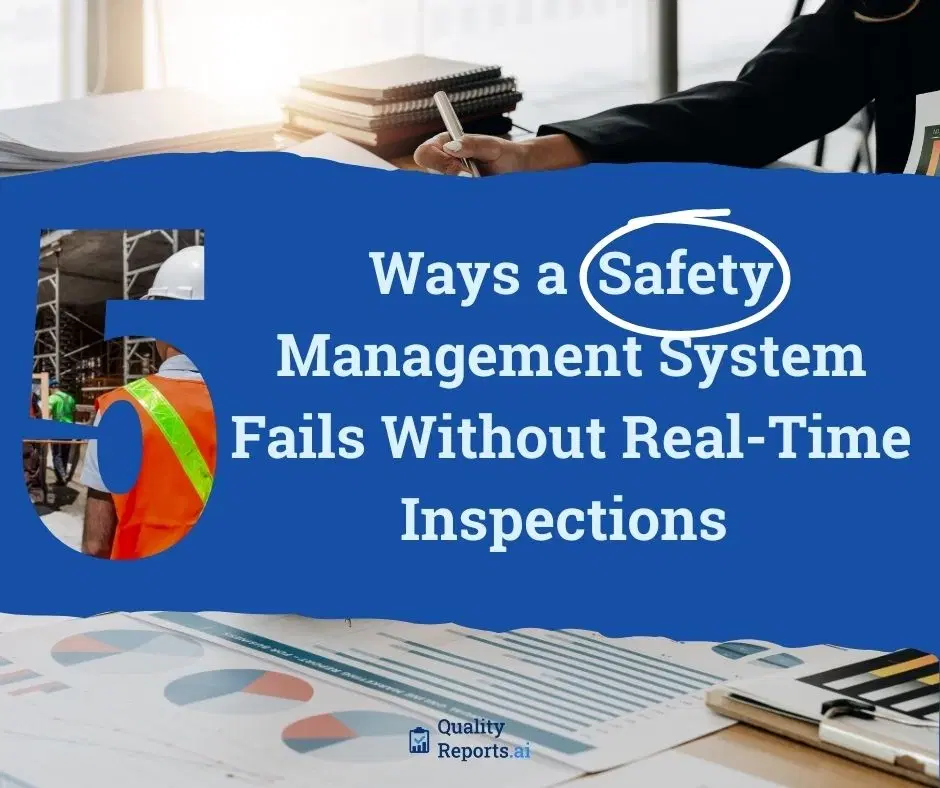
5 Ways a Safety Management System Fails Without Real-Time Inspections
Most companies have some form of safety management system (SMS). Fewer have one that actually works when it matters.
A binder full of policies? That's not protection. Delayed inspection reports? That's not prevention. If your system can't detect issues as they occur or trigger immediate action, it's not a safety program. It's documentation.
And documentation without action won't stop the next near-miss, breakdown, or audit failure.
In this article, we break down five critical ways static or paper-based SMS processes fail to deliver. We also show how digital tools, specifically the Alerts, Schedule, and Analytics features in QualityReports.ai, bridge those gaps and bring safety programs into real time.
Quick Sidebar: What Is a Safety Management System?
A Safety Management System (SMS) is the structure a company uses to control risk and drive safety performance. It typically includes:
- Policies and SOPs
- Risk assessments
- Inspection programs
- Training systems
- Reporting and investigation processes
- Continuous improvement mechanisms
A safety information management system is the digital infrastructure that supports all of the above. Tools like ours at QualityReports.ai provide the real-time connection between policy and practice, making the SMS not just visible, but actionable.
1. No Real-Time Visibility Means Delayed Risk Response
The most common failure of traditional safety systems is simple: they're too slow.
When inspections are done with clipboards and carbon copies, by the time a problem is logged, filed, and reviewed, the risk has already snowballed. Equipment might have failed. A worker might already be injured. Or the opportunity to intervene has long passed.
This isn't just theory, it happens every day. In high-speed environments like lumber mills or truss manufacturing plants, even an hour of delay can result in cascading failures across production, logistics, and compliance.
With QualityReports.ai, every inspection result is instantly available. Failed items trigger automated alerts, notifying managers or safety leads immediately. That means no more "I didn't see the report" or "it was buried on someone's desk." You see it, you respond, you close the loop.
Example:
A saw operator flags excessive vibration in a station. With real-time alerts, maintenance is dispatched before the shift ends, avoiding downtime, potential injury, and a broken machine.
2. Paper Trails Don't Enforce Accountability
Accountability doesn't mean blame, it means visibility.
In a paper-based SMS, it's often unclear:
- Who conducted the inspection?
- Was every checkpoint completed?
- When was it done and what happened after?
Even with the best intentions, manual systems allow things to slip. Missed follow-ups, unchecked hazards, and undocumented fixes are common because there's no system to verify what was done, when, and by whom.
The Schedule feature in QualityReports.ai creates structure and clarity. Inspections are assigned to individuals or teams, with recurrence intervals, due dates, and automated reminders. Managers can immediately see overdue items, missed steps, and incomplete tasks.
Why it matters:
A system that only tracks reports doesn't create change. A system that tracks responsibility drives it.
3. Manual Systems Can't Spot Patterns or Fix Them
A good SMS doesn't just record incidents. It uncovers why they keep happening.
When inspections are logged in isolation, whether on paper or in disconnected files, there's no way to see the bigger picture. You can't answer questions like:
- Which department has the most failed items?
- Are we getting better or worse over time?
- Are corrective actions actually working?
This is where Analytics comes in. With QualityReports.ai, every inspection builds your data set. Trends are automatically visualized over time, by team, location, asset, or category. That lets you move from reacting to preventing and from guessing to knowing.
Example:
You spot a 3-week pattern of inspection failures tied to one machine. It turns out a new operator was skipping setup steps. One retraining session solves the issue permanently.
4. Delayed Communication Creates Duplication and Risk
Here's a common breakdown: The night shift finds a hazard and logs it. The day shift doesn't know. They proceed as usual and the problem escalates.
Without live communication, inspections become time-stamped complaints rather than coordinated responses.
QualityReports.ai integrates comments, alerts, and notifications directly into the inspection workflow. That means when an issue is flagged, the right people know immediately, and they can respond in the same system. Updates are visible, nothing gets lost in translation, and corrective actions are transparent.
Why it matters:
Safety isn't just about finding the problem. it's about fixing it together. Delayed communication leads to rework, missed handoffs, and repeat incidents.
5. No Feedback Loop = No Culture Change
A lot of companies run inspections. Fewer use that data to improve.
If issues are logged but never addressed...
If reports are filed but never reviewed...
If teams flag problems but never hear back...
Then eventually, people stop reporting. Trust erodes. And "safety culture" becomes a box you check, not a value you live.
QualityReports.ai completes the feedback loop. Our dashboards show trends. Alerts confirm follow-up. Reports can be shared in toolbox talks or management reviews. That visibility builds trust. And that trust builds engagement.
Example:
Over six months, near-miss reporting increases 40% because team members see that their flags lead to real action. As engagement rises, incidents drop. That's culture change backed by data.
Final Thought: Don't Let Paper Slow Down Safety
A static SMS gives you paperwork. A real-time SMS gives you protection.
If your current safety process depends on forms that get filed, reports that get read "eventually," and reminders that live in someone's inbox, you're not just outdated. You're exposed.
QualityReports.ai helps you:
- Catch risks early with live Alerts
- Keep inspections on time with Scheduled workflows
- Find patterns with Analytics that drive real improvement
It's safety that's proactive, not reactive. And that's what your team, and your operation deserve.
See it in action.
Start a free trial or book a demo at QualityReports.ai